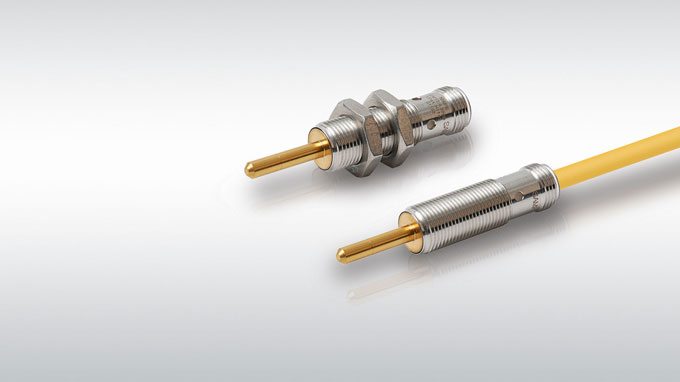
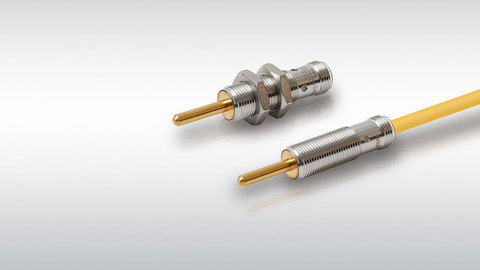
The TiN-coated sensor probe is extremely abrasion resistant
Weld Nut Sensor Detects M5 Nuts
16/16 – Turck is adding devices with a wear-free TiN-coating, Ø4 mm design and pigtail connection cable to its range of weld nut sensors
Mülheim, October 27, 2016Turck is adding variants with a Ø4 mm sensor probe to its range of weld nut sensors. This makes the detection of missing M5 nuts before welding even simpler. Turck has also improved the abrasion resistance of its weld nut sensors with optional titanium nitride coatings (TiN). As steel plates and nuts have to be placed onto these sensors before welding, they are exposed to a high degree of friction over their entire service life. The TiN coating offers protection against wear, scratches and accumulated welding spatter.
The sensors offer the user a favorable and reliable way of checking the correct seating of weld nuts. The workpiece and the weld nut required for welding are placed on the new sensor probe. Alternative ways of checking the presence of nuts using laser sensors or camera technology are considerably more complex and also more prone to faults. Unlike these alternatives, the weld nut sensors are easy to install and can be configured to detect the nuts with just a few button presses of the associated teach adapter. The weld nut sensors are also weld resistant – and likewise the pigtail cables.
In addition to the TiN-coated variants, Turck is also still offering the weld nut sensors in conventional stainless steel or brass housings. The four designs are used to detect nuts with M5 to M20 threads. On the connection end, the user can also select devices with M12 connectors in addition to the new pigtail variants.
Turck is adding variants with a Ø4 mm sensor probe to its range of weld nut sensors. This makes the detection of missing M5 nuts before welding even simpler. Turck has also improved the abrasion resistance of its weld nut sensors with optional titanium nitride coatings (TiN). As steel plates and nuts have to be placed onto these sensors before welding, they are exposed to a high degree of friction over their entire service life. The TiN coating offers protection against wear, scratches and accumulated welding spatter.
The sensors offer the user a favorable and reliable way of checking the correct seating of weld nuts. The workpiece and the weld nut required for welding are placed on the new sensor probe. Alternative ways of checking the presence of nuts using laser sensors or camera technology are considerably more complex and also more prone to faults. Unlike these alternatives, the weld nut sensors are easy to install and can be configured to detect the nuts with just a few button presses of the associated teach adapter. The weld nut sensors are also weld resistant – and likewise the pigtail cables.
In addition to the TiN-coated variants, Turck is also still offering the weld nut sensors in conventional stainless steel or brass housings. The four designs are used to detect nuts with M5 to M20 threads. On the connection end, the user can also select devices with M12 connectors in addition to the new pigtail variants.