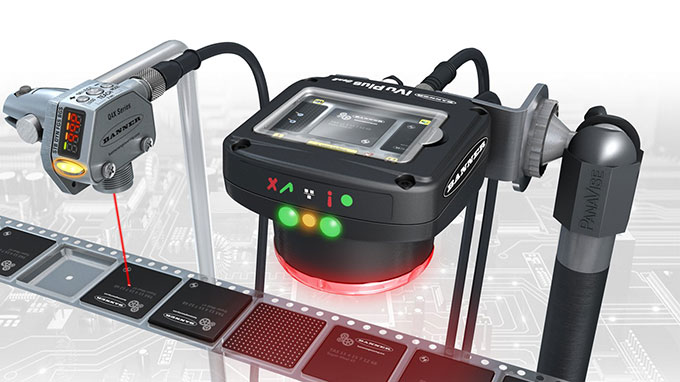
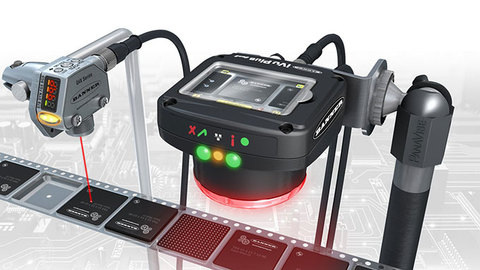
Error Proofing for Integrated Circuit Chips Loaded in Pocket Tape
Join the strengths of the Q4X and iVu vision sensor for a triple inspection of IC Chips
Integrated circuit (IC) chips are tested before installation onto a circuit board. After they pass quality tests, they are placed into a pocket tape and spooled onto a reel. The tape and reel make transport and storage for such small components easy and simplify the way that the product is fed into assembly machines.
Each IC chip is placed onto the pocket tape by a high-speed machine. Incorrectly oriented chips will result in improper installation onto a circuit board. There are three common failure modes with pocket tape: no chip in the pocket, two chips in the pocket, and one chip upside down in the pocket. To prevent these errors, each chip’s presence and orientation needs to be confirmed before it is sealed in the pocket tape. Multiple sensors are often used to identify these failures. Supporting multiple sensors can drive up expenses and lead to increased downtime required for maintenance and installation.
Your Benefits
- More thorough detection of errors before installation on circuit boards
- Confirmation of writing orientation on IC chips
- Reduced cost using fewer sensors to solve the application
The Q4X laser distance sensor from Banner Engineering can complete all the functions previously performed by multiple sensors. This versatile sensor can be taught to recognize items at a specific distance, meaning that it can tell the difference between no chip, one chip, or two chips, in each slot as the chip passes. If the sensor reads the correct distance, this means that one chip is placed into the pocket tape. If the distance read is too short, this means a duplicate chip has been placed on top of the first chip. If nothing is sensed, or the distance is too long, this indicates a missing chip. Also, used in dual mode, the Q4X will also detect differences, in contrast, to determine if a chip is right side up or right side down. The Q4X can detect all of these conditions (missing, duplicate, or right side down chips) and trigger an indication that operator attention is required.
In some instances, text or images, such as logos or lot codes, may be printed on the chips and it may be necessary to have these features all oriented that same direction. An iVu vision sensor can be used to determine the correct orientation of the writing by utilizing the powerful match tool. If there is no match, an operator is notified of the fail.
In an industry where components are required to be tremendously small, errors and a bad product can be challenging to detect. Banner offers solutions that fit the needs of these applications. By using the Q4X and iVu vision sensor simultaneously, the manufacturer can detect three different types of errors and confirm writing orientation on integrated circuit chips. By using fewer devices, companies are saving time and money with an easy to use solution.
- Automotive
- Press Shop – Tool Identification
- Sheet Metal Thickness Measurement
- Body Shop – Welding Nut Detection
- Paint Shop – Skid Identification
- Final Assembly – Robot Assembly
- Final Assembly – Diagnosis of Leaks
- Area Guarding for Robotic Cells
- Tier 1 – Bumper Identification
- Powertrain – Contactless Verification
- Inspection of Tips on a Welder
- Body Detection in Automobile Production
- Item-level Detection with UHF RFID
- Supply of cooling lubricant in machine tools
- Manual Feeding in Weld Cell
- Controlling hydraulic pressure in pressing plants
- Measuring process pressure on scissor lifts
- Detecting Black Parts on Black Door Panel
- Moonroof Clear Glass Detection
- Long-Range Inspection in Automotive Assembly
- Rubber Washer Detection on Engine Block
- Engine Block Part-In-Place Detection
- Electric Vehicle Detection in Charging Station
- Vehicle Detection in a Self-Serve Car Wash
- Success Stories
- RFID Guides AGV in Suspension Production
- IO-Link Wired Silencer Production
- Workpiece Carrier Identification in Rear Vent Production
- Weld Nut Sensing
- RFID Traceability
- RFID in Engine Production
- Bumper Production with Identification
- Solutions for Paint Shops
- Welding and Assembly Sensors
- Angle Sensors for Assembly Systems
- Tool Identification
- RFID Identification of Injector Nozzles
- RFID in the Body Shop
- IO-Link Eases Differential Gear Production
- Pick-to-Light for Bumper Assembly
- RFID and I/O modules for Safe Tool Changes
- Ply Orientation Inspection
- Chemical
- Detection of Pigs
- Remote Signal I/O
- Easy Connection of Field Devices
- Signal Processing with System I/O in the Control Cabinet
- Remote Tank Level Monitoring with DX70
- Signal Separation with Interface Technology in the Control Cabinet
- Identification of Hose Connections
- Efficient Monitoring of Cabinets in the Field
- Monitoring of Quarter Turn Actuators
- Planning and Assembly of System Solutions
- Success Stories
- I/O System Excom Creates Space in the I&C Rooms
- Zone 2 and 22 RFID
- Efficient Testing Control
- Intrinsically Safe Field Communication
- Process Control System Partnership
- Hazardous Area Remote I/O
- Dual Valve Position Feedback
- Flexibility with Fieldbus
- Asset Management with Remote I/O
- Correct Positioning with RFID in Carbid Production
- Fast conversion in restricted space
- Energy
- Food and Beverage
- Dough Height Inspection for Accurate Measurement
- Dough Thickness Control in Rolling Machines
- Leading Edge Detection of Plastic Container
- Date/Lot Code Verification
- Identification of Food Containers
- Detection of Valve Position
- Container Check
- Barcode Reading on Depalletizer Station
- Reliable Cap Orientation Verification in Aseptic Areas
- Detection of Pipe Elbows
- Clear and Tipped Bottle Detection on Depalletizer
- Clear Plastic Bottle Detection
- Identification of Chocolate Moulds
- Frozen Food Packaging Label Inspection
- In-Line Bottle Accumulation on Single Filer
- Detecting Refrigerated Breakfast Rolls on a Multi-Lane Conveyor
- Success Stories
- Track and Trace in Meat Production with RFID
- Contact-free Encoder in Potato Production
- UHF RFID in Food Distribution Center
- RFID for Chocolate production
- Distributed I/O for Food Equipment
- Remote I/O for Distilleries
- RFID and Autoclaves
- IP67 Power Supplies for Conveyors
- Transparency in Chocolate Manufacturing
- Identification in Food Product Storage
- Mobile Equipment
- Distribution Lines for Field Sprayers
- Loading Dock Occupancy Monitoring
- Measuring the Ground Clearance on a Field Sprayer
- Monitoring Railcars Wheels Wirelessly
- Reach Stacker Status With Bright Lighting Indicators
- Angle Measurement on a Field Sprayer
- Determining the Boom Angle Position
- Material Flow Monitoring on a Combine Harvester
- Vehicle at Loading Dock
- Equipment Compartment Illumination on Fire Engines
- Wireless Forklift Signaling
- STS Collision Avoidance
- Two-Axis Tilt Measurement on a Combine Harvester
- Collision Protection on Reach Stackers
- Success Stories
- Position Measurement with RFID and Encoder
- Speed Control via Radar Sensor QT50
- RFID Guides AGV in Suspension Production
- Block I/O Modules on Super Yacht
- Wear-free Encoder on Hopper Dredger
- I/O for Dust Suppression
- Cabinet Cooling
- Quick Disconnect Connectivity
- Automation Solutions for Extreme Cold
- Remote I/O for Cranes
- Rugged Heavy Metal Lifting
- Rollercoaster Positioning
- Mobile Machinery Solutions
- Exact Height Positioning
- Critical Angle Sensing
- Angle Sensor Detects Platform Lift
- Predictive Maintenance of Machine Parts at Port-Based Coal Conveying Facility
- Oil and Gas
- Packaging
- Identification of Printing Color Cartridges
- Reliable Operation of Machines
- Monitoring of Caps in Filling Lines
- Monitoring Changeover Processes
- Identification of Test Bottles
- Level Monitoring of Ground Coffee
- Box Insert Detection
- Level Detection in Vessels
- Carton Dimensioning
- Detection of Transport Containers
- Clear Container Detection
- Correct Label Verification
- Detecting Different Size Packages on a Conveyor
- High-Speed 2D Barcode Inspection
- Multicolored Reflective Package Detection
- Plastic Roll Diameter Measurement
- Tube Positioning Using a Registration Mark
- Vertical Form Fill Seal Machine Solutions
- Success Stories
- Pharma
- Monitoring of Quarter Turn Actuators
- Detection of Pipe Elbows
- High-Speed Tablet Counting With Fiber Amplifier
- Remote Signal I/O
- Planning and Construction of Super Skids
- Easy Connection of Field Devices
- I.V. Bag Liquid Detection
- Identification of Portable Tanks
- Identification of Cryovessels
- Identification of Mobile Containers
- Liquid Level Monitoring In A Large Tank
- Identification of Mobile Containers with Handheld Devices
- Identification of Hose Connections for Precursors
- Identification of Hose Connections in Sterile Areas
- Identification of Hose Connections in Ex Zone 1
- Identification of Big Bags and Bioreactors
- Identification of Single-Use Applications
- Success Stories
- Semiconductor
- Arc Flash
- Error Proofing with RFID
- Semiconductor Process Tool Illumination
- Wafer Center Detection with Fiber Amplifier DF-G2
- Adhesive Detection on PCB Assembly
- Great Detail Inspection for Mobile Electronic Devices
- Error Proofing for IC Chips loaded into Pocket Tape
- Presence and Orientation of IC Chips Seated in Nests
- Detection of Hard Disks
- Multiproduct Light-Guided Assembly Station